Overhead Electromagnet
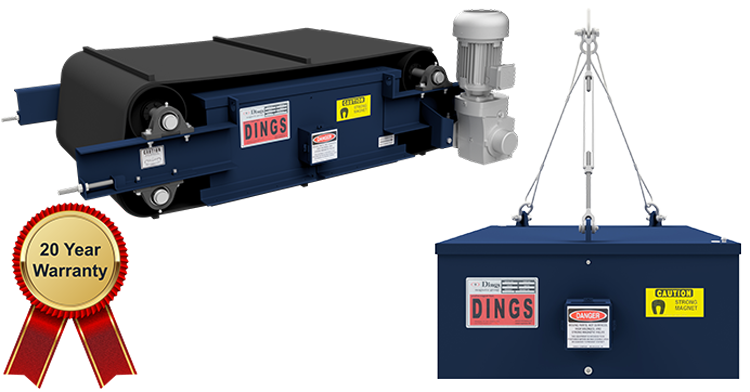
Overhead Electromagnets are suspended over conveyor belts and vibratory feeders. They are designed to magnetically lift ferrous metals out of bulk material which ensures product purity and protects processing equipment. Any ferrous metal that is attracted to the magnet face is either automatically and continuously removed with our self-cleaning models or held in place on stationary models until the magnet is turned off. Our Overhead Electromagnets remove damaging ferrous tramp metal, which can cause costly repairs and downtime.
20-Year Warranty on Coil Burnout for Overhead Electromagnets
THE BEST WARRANTY IN THE INDUSTRY!
Our electromagnet coils are wound with an anodized aluminum strap; an exclusive design that generates more magnetism than any other electromagnet on the market and exceeds Class “H” insulation rating! This design outlasts and outperforms “conventional” round wire coils that can lead to coil burnouts.
Dings Electromagnetic Coils
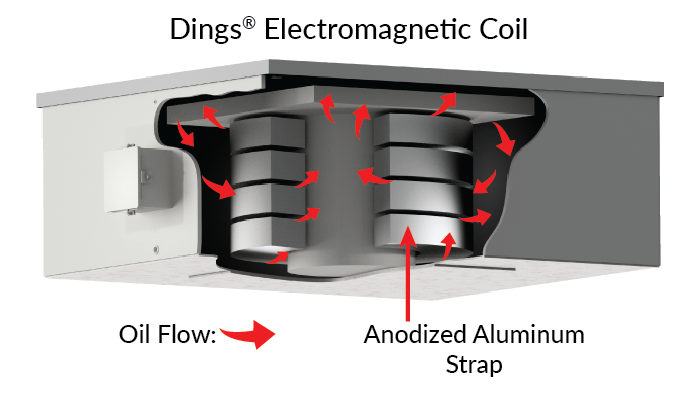
Dings electromagnetic coils are wound with an anodized aluminum strap; an exclusive design that generates more magnetism than any other electromagnet on the market and exceeds Class “H” insulation rating! This design outlasts and out-performs copper wire with polymer insulation or bare aluminum with Nomex® insulation.
Dings electromagnetic coils stay cooler – operating at a much lower temperature. Since electromagnets perform best at lower operating temperatures, this design ensures Dings electromagnets are stronger and more efficient. With “conventional” round wire coils, inside turns are not cooled evenly and product hot spots that damage coils. Each turn of the Dings electromagnetic coil is exposed to oil-cooling and is in constant contact with oil, therefore, eliminating the need for an oil expansion tank. Oil is free to flow around and in between each coil to maximize cooling effect.
- 20-Year Warranty on coil burnout
- No insulation needed – eliminating the major cause of coil failure (insulation breakdown)
- More magnetism and separating power – generated by extra turns
- Each turn is exposed to oil-cooling (assuring a stronger, more efficient magnet)
- Eliminates the need for external oil expansion (less pipes or tanks that can easily be damaged)
Self-Cleaning Magnetic Separators
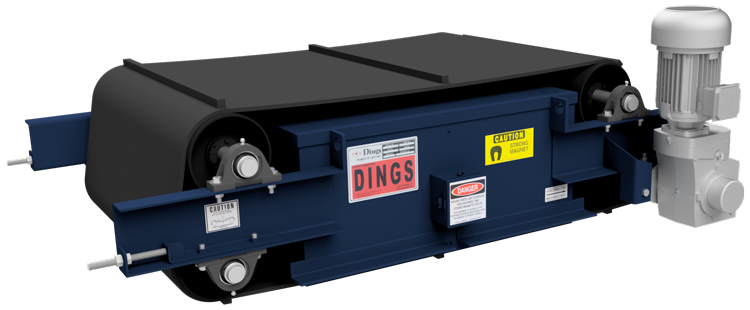
Self-Cleaning Magnetic Separator Models have a belt that continuously travels across the face of the magnet body to automatically discharge attracted ferrous metal away from the magnetic zone. These powerful models come equipped with a heavy-duty rubber belt to remove ferrous metal from the material stream. Other cleat styles and sizes are available for use in different ferrous recovery applications. To drive the magnetic belt, a direct gear motor is used and also available in special voltages.
SELF-CLEANING MAGNETIC SEPARATOR FEATURES
- 20-Year Warranty against coil burnout – the best in the industry!
- Expansion of high dielectric strength cooling oil takes place inside the magnet box. No external oil tank or additional plumbing is required. A pressure relief valve prevents moisture from entering the magnet box. The electromagnet is filled with cooling oil containing antioxidants that improve service life for operation under severe conditions at the factory prior to shipment.
- Easy access to oil level, oil drain and oil fill plugs
- Full stainless-steel bottom plate with extra stainless-steel center wear plate in the main impact area provides longer life.
- IP56 AGMA Class II Motor
- Non-endless multi-ply (heavy duty) rubber belt with cleats hot vulcanized to base for superior adhesion.
- Crown curved pulleys for easy belt tracking
- NEMA 4 terminal box provides protection the elements.
- Inline or Crossbelt mounting positions
- Stainless-steel deflector extends the belt life and minimizes cleaning (crossbelt mounting only)
OPTIONS
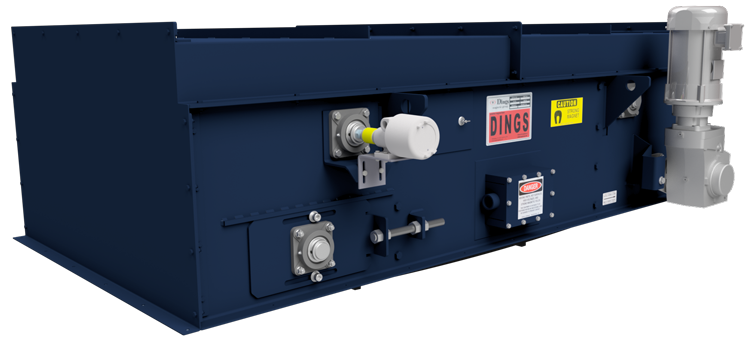
Dust Cover
Totally enclosed, dust-tight constructed enclosure allows integration into dust collection systems.
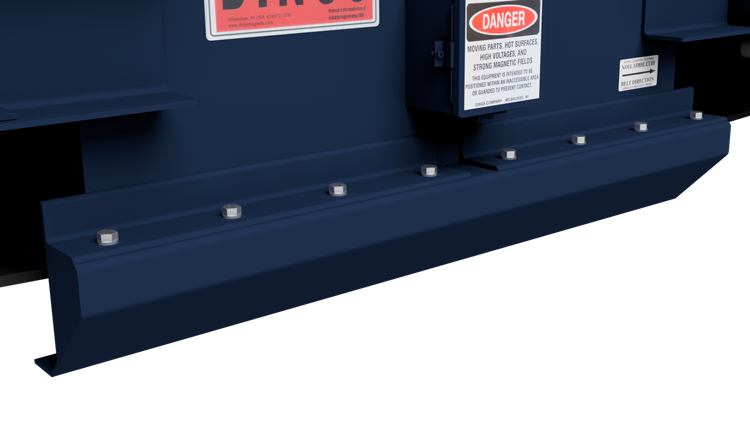
Crossbelt Deflectors
The crossbelt deflector is standard and mounted to the magnet box perpendicular to the conveyor. It is used to prevent conveyed material from getting jammed between the magnet box and the self-cleaning belt.
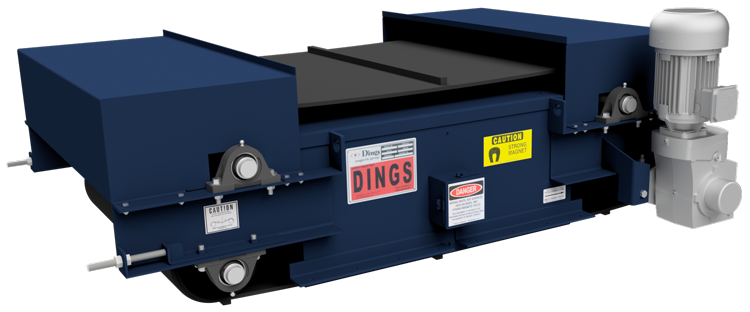
Pulley Guards
The pulley guard is a safety option that prevents access to the rotating pulleys, ensuring safety of personnel.
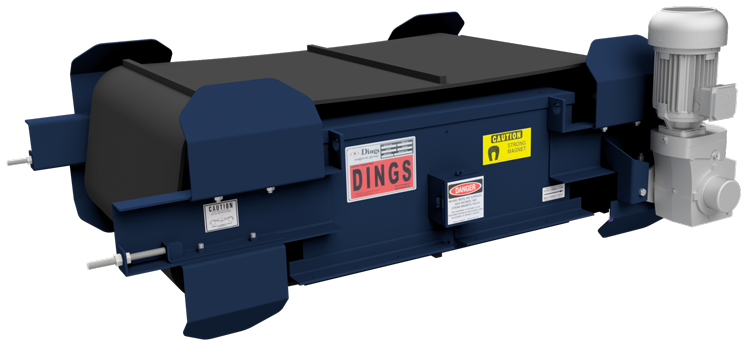
Pinch Point Guards
Pinch point guards prevent access to a point on the equipment where personnel can get caught in between moving parts.
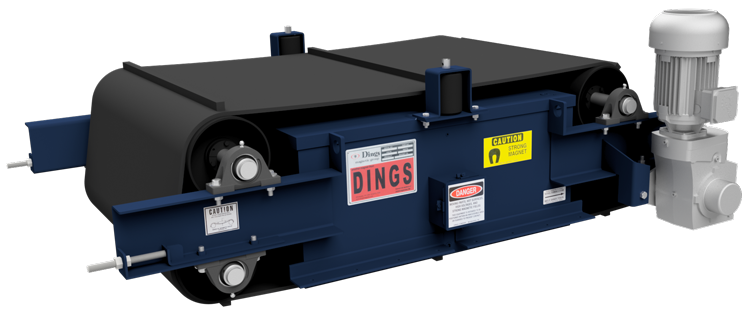
Belt Guide Rollers
They assist in the prevention of belt damage due to poor belt tracking. They are typically used when magnets are suspended at a significant angle.
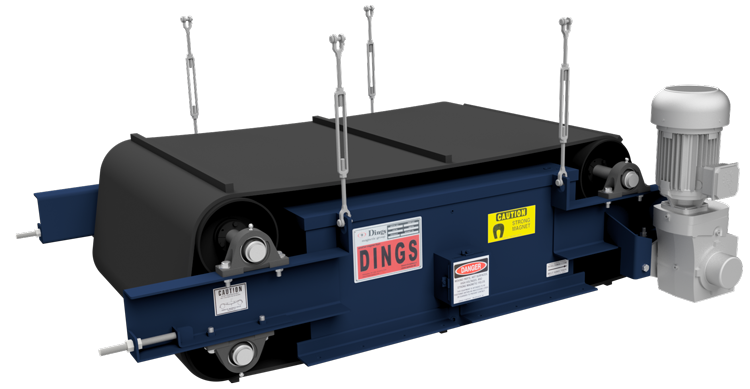
Turnbuckles
Facilitates the final adjustment of the magnet’s suspension height.
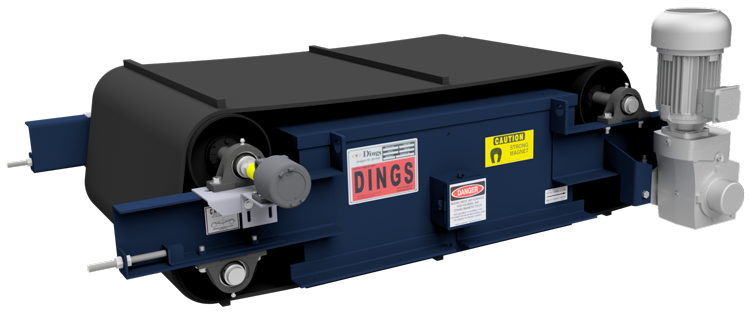
Zero Speed Switch
This motion control safety sensor signals when the magnetic separator belt has stopped moving.
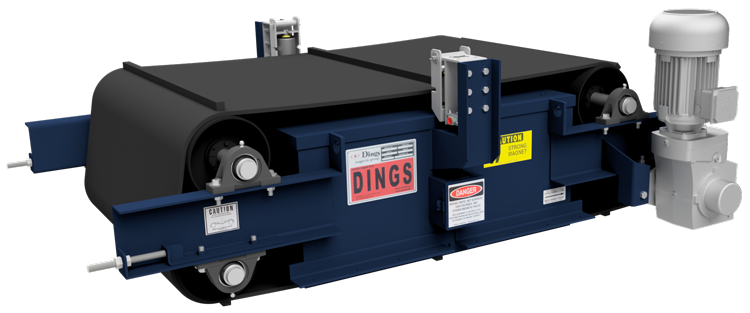
Belt Alignment Switches
This motion control safety sensor is used to monitor belts for misalignment. If the belt has tracked too far to one side of the magnet, the misalignment switch will shut the belt down preventing costly repairs and downtime.
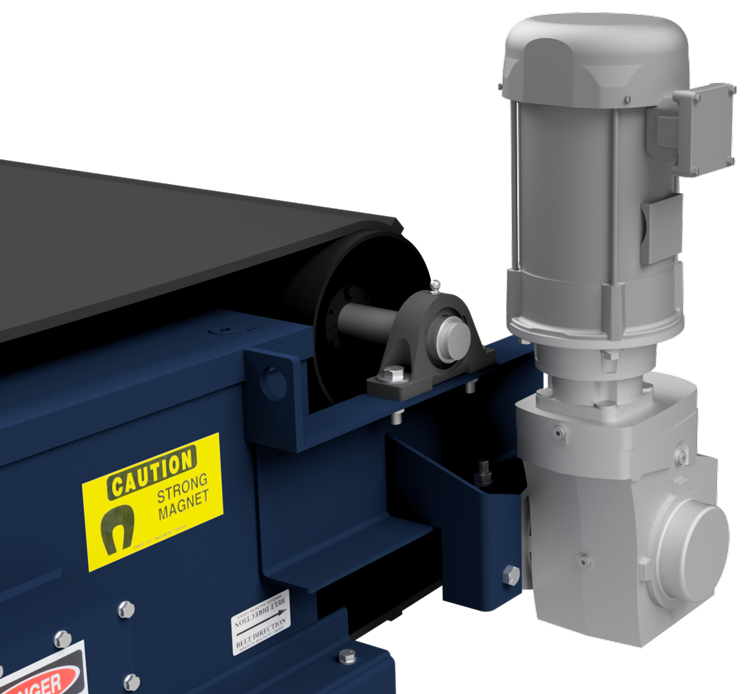
Explosion Proof Motors
Explosion proof motors are UL certified electric motors that meet the hazardous locations needs of an application.
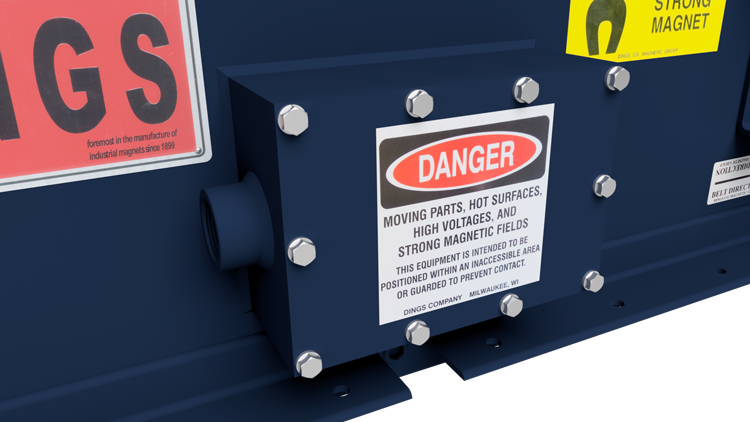
Explosion Proof
Terminal Box
A terminal box designed and built to follow hazardous locations construction criteria.
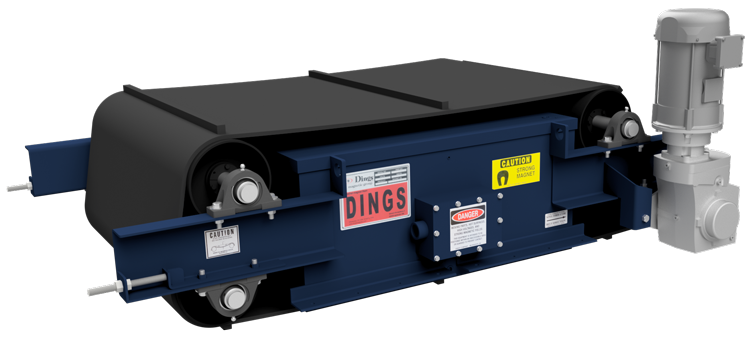
Hazardous Locations Model
This model magnetic separators are designed and built to follow hazardous location environment criteria.
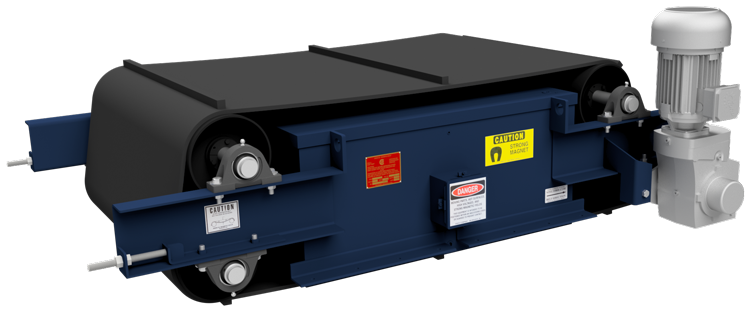
CSA Approved
These magnetic separators are certified to meet CSA (Canadian Standards Association) standards for use in Canada.
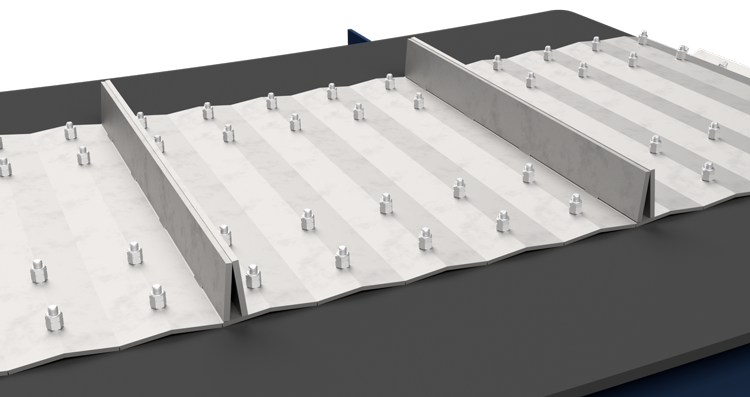
Dings Armor-Clad
Dura-belt
A metal clad belt developed by Dings Co. Magnetic Group as a long-life magnet cleaning belt for installations where many sharp-edged iron objects are encountered—especially useful when recycling concrete with rebar. Continuous impacts from sharp steel can cause rapid wear on standard cleaning belts. The entire impact area on a ‘Durabelt’ is protected with an armored barrier of thick stainless-steel pads. The self-cleaning belt travels continuously around the magnetic separator, automatically discharging the attracted ferrous. Individual plates can be easily replaced in the field, saving costs on belt replacement and reducing downtime.
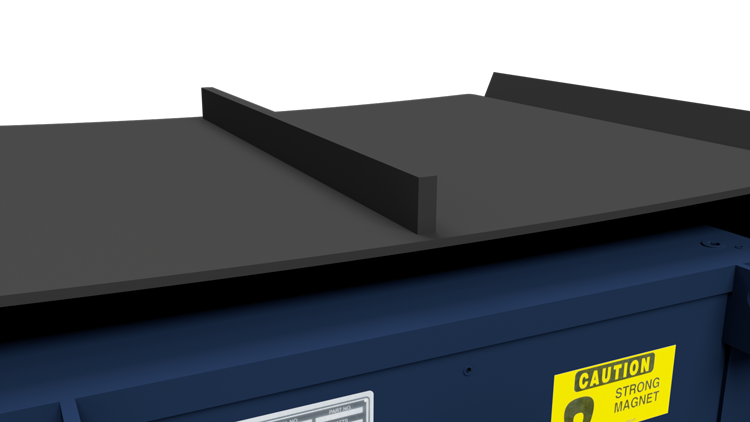
3-Inch Rubber Cleats
Vulcanized cleats typically used in recycling applications where large ferrous metal is better carried away by 3-inch high cleats versus our standard 1-inch high cleats.
High Temperature Belt
These belts are designed to withstand temperatures of up to 200ºF and are certified to meet CSA (Canadian Standards Association) standards for use in Canada.
Special Motor Voltages
Special motor voltages are available to meet any specific application requirements.
Custom Designs
Our magnetic solutions experts can custom design any equipment to meet your specific application needs.
Stationary MAGNETIC SEPARATORS
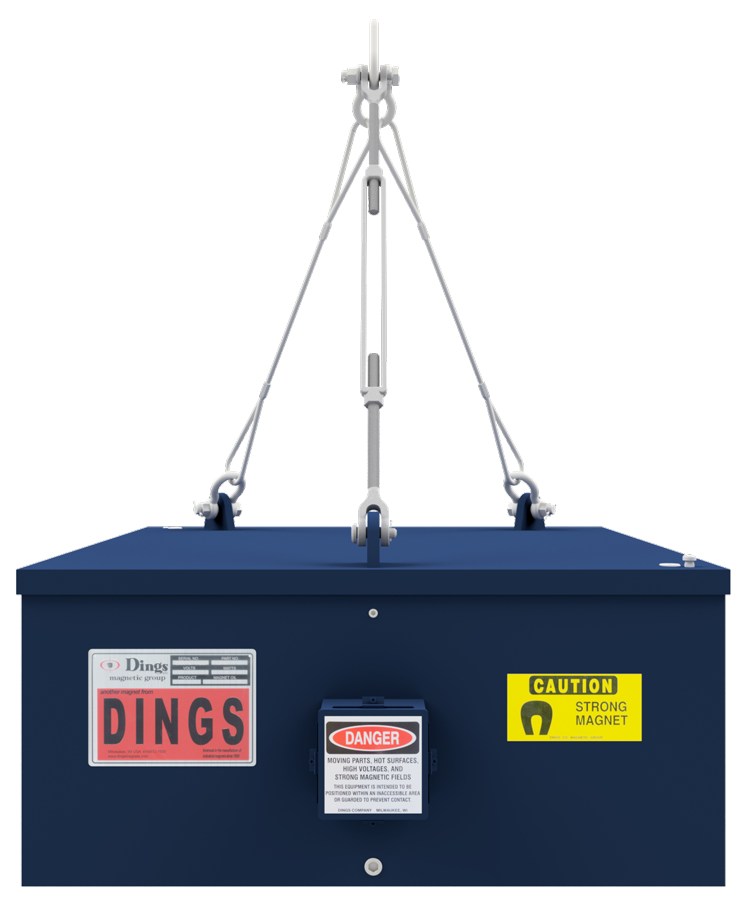
Stationary Magnetic Separator models are maintenance-free (other than maintaining oil in the electro) with no moving parts (no lubrication, no tightening or replacing of hardware needed). Ferrous metal is pulled out of the material stream to the face of the magnet and held in place until the magnet is turned off. Designed for easy installation; this model comes with a 3-point suspension system that includes two cables and one turnbuckle connected to a common bull ring. Adjustment of the magnet suspension angle is easy and only involves adjustment of the turnbuckle. There is no measuring, shortening, lengthening or cutting of cable required. These magnets are constructed with a stainless-steel bottom wear plate over the impact area.
FEATURES
- 20-Year Warranty against coil burnout – the best in the industry!
- Expansion of high dielectric strength cooling oil takes place inside the magnet box. No external oil tank or additional plumbing is required. A pressure relief valve prevents moisture from entering the magnet box. The electromagnet is filled with cooling oil at the factory prior to shipment.
- Stainless-steel bottom plate, steel side plates and backplate
- Additional wear plate provides extra protection for the magnet impact area.
- Easy installation
- Maintenance-free
OPTIONS
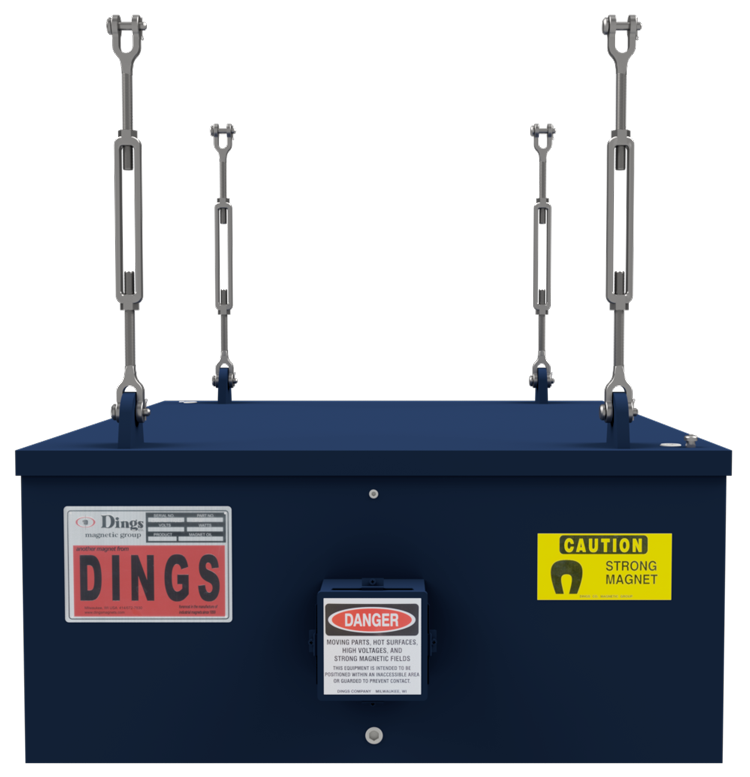
4-Point Suspension System
Additional suspension points allow for more adjustment options.
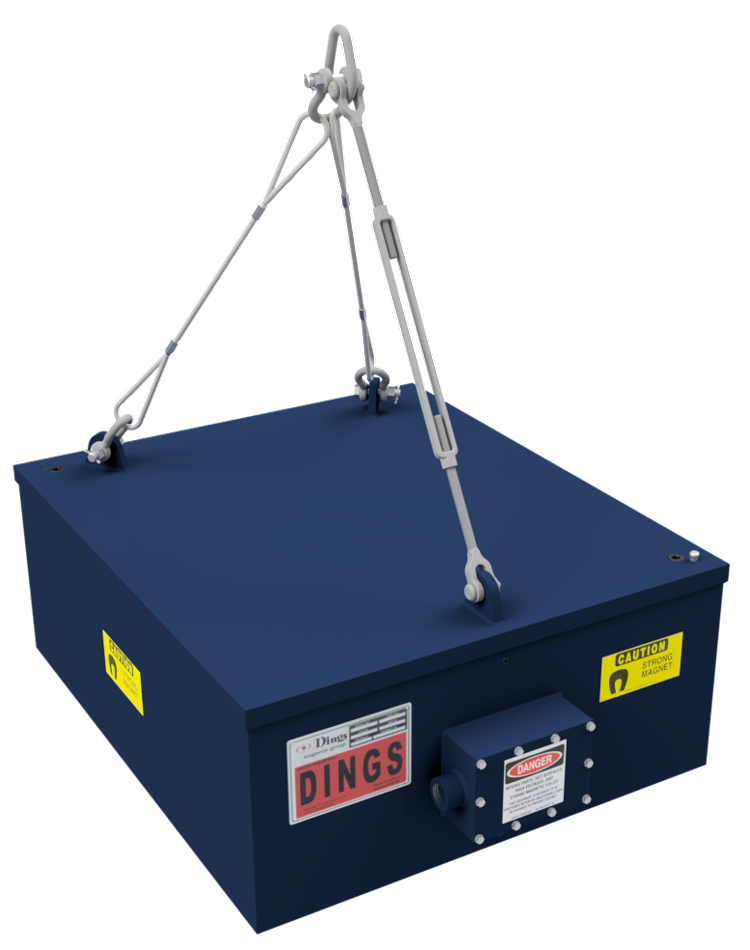
Explosion Proof
Terminal Box
A terminal box designed and built to follow hazardous locations construction criteria.
Custom Designs
Our magnetic solutions experts can custom design any equipment to meet your specific application needs.
Severe Duty Design Magnetic Separators
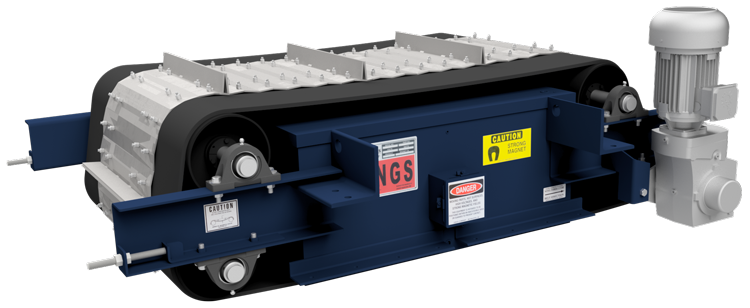
Dings Severe Duty Design models are tough, rugged version of the Self-Cleaning Electromagnet. They are specifically designed for severe duty applications such as concrete recycling. They are built to withstand the harshest environments. The Severe Duty Design comes equipped with the Dings Armor-Clad ‘Durabelt’ that prevents the rubber belt from being pierced by pointed rods such as rebar, a heavy-duty drive assembly, lagging on the drive pulley and reinforced suspension/mounting arrangement.
FEATURES
- 20-Year Warranty against coil burnout – the best in the industry!
- Expansion of high dielectric strength cooling oil takes place inside the magnet box. No external oil tank or additional plumbing is required. A pressure relief valve prevents moisture from entering the magnet box. The electromagnet is filled with cooling oil at the factory prior to shipment.
- Easy access to oil level, oil drain and oil fill plugs.
- IP56 AGMA Class II Motor
- NEMA 4 terminal box provides protection against ingress of solid foreign objects
- Inline or Crossbelt mounting positions
- Stainless-steel deflector extends the belt life and minimizes cleaning (crossbelt mounting only)
- Armor-clad ‘Dings Durabelt’ – see description above;
- Lagging on the drive pulley
- Individual plates or cleats can be easily replaced in the field.
OPTIONS
Custom Designs
Our magnetic solutions experts can custom design any equipment to meet your specific application needs.
MRF (Material Recovery Facility) Magnetic separators
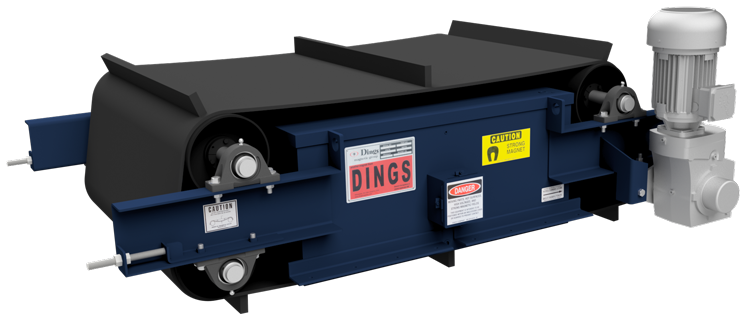
The MRF (Material Recovery Facility) Self-Cleaning Magnetic Separator model features 3-inch tall rubber cleats on a tough vulcanized belt. This serves to sweep away large diameter cans that might not be removed with the standard 1-inch high cleat.
FEATURES
- 20-Year Warranty against coil burnout – the best in the industry!
- Expansion of high dielectric strength cooling oil takes place inside the magnet box. No external oil tank or additional plumbing is required. A pressure relief valve prevents moisture from entering the magnet box. The electromagnet is filled with cooling oil at the factory prior to shipment.
- Easy access to oil level, oil drain and oil fill plugs
- IP56 AGMA Class II Motor
- NEMA 4 terminal box provides protection against the elements.
- Inline or Crossbelt mounting positions
OPTIONS
Custom Designs
Our magnetic solutions experts can custom design any equipment to meet your specific application needs.
SWMS (Solid Waste Management System) Magnetic separator
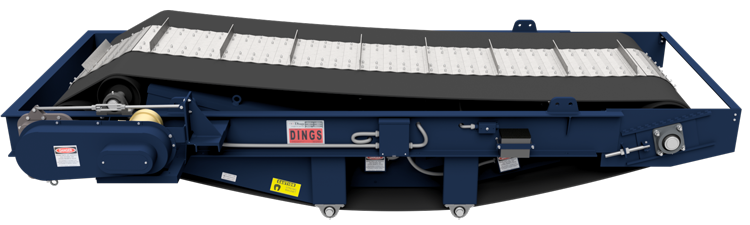
The SWMS (Solid Waste Management System) Magnetic Separator Model is a powerful, highly selective magnetic separator designed exclusively for separating steel from shredded solid waste. It is used in plants that reclaim steel and produce refuse derived from fuel. This patented-designed system is constructed with separate mounted electromagnets (single, double or triple options available) to have a long and deep penetrating magnetic field, a Dings Armor-Clad ‘Durabelt’, a heavy-duty drive assembly, lagging on the drive pulley and reinforced suspension/mounting arrangement. The SWMS (Solid Waste Management System) operates with vigorous actions to produce clean, salable steel.
FEATURES
- 20-Year Warranty against coil burnout – the best in the industry!
- Expansion of high dielectric strength cooling oil takes place inside the magnet box. No external oil tank or additional plumbing is required. A pressure relief valve prevents moisture from entering the magnet box. The electromagnet is filled with cooling oil at the factory prior to shipment.
- Easy access to oil level, oil drain and oil fill plugs.
- IP56 AGMA Class II Motor
- NEMA 4 terminal box provides protection against the elements.
- Armor-clad ‘Dings Durabelt’
- Lagging on the drive pulley
- Individual plates or cleats can be easily replaced in the field.
OPTIONS
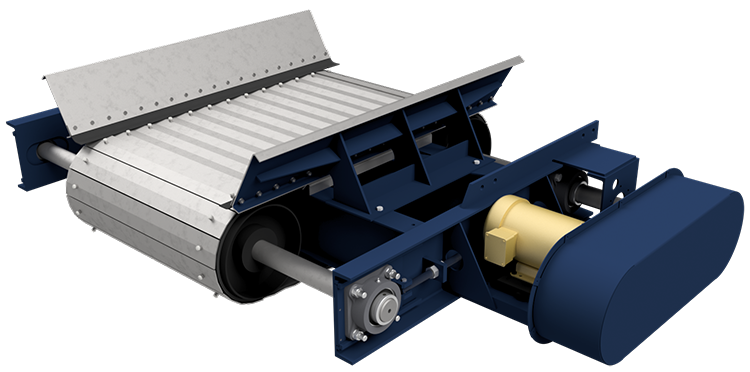
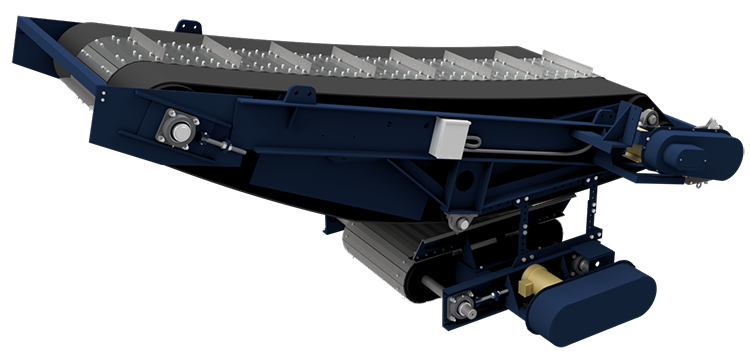
Under-Slung Transfer Conveyor
(included with 2 stage SWMS Model)
This under transfer conveyor retains attracted magnetics in the system until final discharge while also introduces a steel cleaning action. Position of conveyor is adjustable and is equipped with a Dings Armor-Clad ‘Durablet’, skirts, lagging on the drive pulley.
Custom Designs
Our magnetic solutions experts can custom design any equipment to meet your specific application needs.
Inline vs. Crossbelt Mounting Positions
Dings overhead electromagnets are suspended over conveyor belts or vibrator feeders in two configurations: Inline and Crossbelt.
Inline Mounting Position
Inline orientation is a more efficient
mounting position than Crossbelt over the conveyor. With an inline mounted magnet, as the material is discharged from the conveyor it becomes airborne. This liberates the tramp metal making it easier to separate because it doesn’t need to be pulled through the material burden. This along with its lower required suspension height sometimes
permits the use of a smaller more economic magnet in comparison to cross-belt over the conveyor orientation. Inline Magnets are used in conjunction with a splitter to ensure
proper separation between burden material and tramp metal.
Crossbelt Over Conveyor
In a cross-belt over the conveyor belt mounting position the electromagnet is installed at a right angle to the travel direction of the material on the belt. Tramp metal is collected by the magnet and discharged by the magnet’s self-cleaning belt into a collection bin along side the conveyor. This orientation is commonly used when the magnet is being installed in an easily accessible area on an existing conveyor.
Crossbelt Over Head Pulley
Several factors make the cross-belt over the head pulley orientation a more efficient option than mounting over the belt. The first one is the conveyor belt flattens as it reaches the pulley allowing for a reduced suspension height. Secondly, as the material leaves the conveyor it becomes airborne, making it easier to separate because the tramp metal doesn’t need to be pulled through the material burden. These factors also
sometimes permit the use of a smaller more economic magnet. Magnets installed in this position are often used in conjunction with a splitter.