For timber recycling and other biomass products such as wood chips and feed pellet the need for metal separation is twofold. First, providing your customers with the product purity they expect. Second, protecting valuable processing equipment that’s made for cutting and shredding organic material, not metal.
However, when it comes to which type of magnetic separator, that depends on the specifics of your process. What type of product are you running? How often are ferrous metals encountered in your product? What is your burden depth and throughput? What type of ferrous contaminants are common? These questions and more can be decisive in what magnetic separator solution is best for your application.
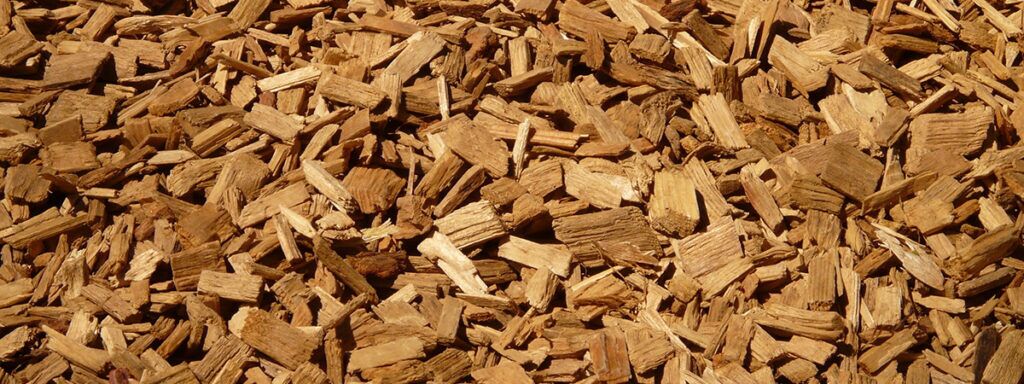
Overhead Magnetic Separators
Overhead magnetic separators, sometimes referred to as overband or overbelt magnets, are often the best solution for removing ferrous contaminants and damage causing tramp metal in most situations.
Permanent Magnets and Electromagnets
Overhead Permanent Magnetic Separators
Overhead permanent magnetic separators always have a magnetic field and don’t require any outside energy to produce it. Permanent magnets, while less expensive than their electromagnet counterparts, come with a series of benefits and drawbacks that determine which applications they are suitable for. For one, they are more space efficient. This smaller size makes them ideal for use in tight spaces. However, this means they are at their best when used in applications with lighter burden depths and smaller belt widths. Something to note when using a permanent magnet, because the magnetic field is always active, ferrous materials must be removed either manually or by use of a self-cleaning belt or other removal mechanism.
Overhead Electromagnetic Separators
Electromagnets use electricity flowing through a coil structure wrapped around an iron or steel core to create their magnetic field. Because of this, overhead electromagnetic separators allow greater control over the presence of its magnetic field. By simply cutting the power ferrous material will be released giving an electromagnet an advantage over the use of a permanent magnet in some situations. The deep toroidal shape of the magnetic field produced by an electromagnet can make it the magnet of choice for troughed belt conveyors or applications with heavier burden depths.
Self-Cleaning and Stationary Magnets
Overhead Self-Cleaning Magnetic Separators
If ferrous impurities are prevalent in your application a self-cleaning model might be best. A self-cleaning magnetic separator uses a multi-ply rubber belt with 1-inch vulcanized cleats that travels across the magnet’s face automatically discharging ferrous material saving time and labor costs. In applications where, sharp tramp metal is common, like heavy gauge nails, that can damage the self-cleaning belt an optional armor-clad Dings “Dura Belt” of stainless-steel pads and cleats is also available.
Overhead Stationary Magnetic Separators
If tramp metal is rare in the process but intolerable, an overhead stationary magnet can be an optimal choice. Without having to accommodate for the sag of a self-cleaning belt in the suspension height, use of a smaller more economical magnetic separator may be possible. Stationary magnetic separators also don’t have moving parts or drive motors that can break down. This saves labor and repair costs while minimizing down time.
Magnetic Head Pulley Separators
Magnetic pulleys are non-electric, self-cleaning magnetic separators that operate as head pulleys on conveyors to separate iron impurities from conveyed product. As the product is discharged from the conveyor, non-magnetic material follows its normal trajectory off the belt while ferrous clings to the magnetic head pulley until it is released under the conveyor as the ferrous metal leaves the pulley’s magnetic field.
Under certain situations, using a magnetic head pulley for your application can have advantages when compared to an overhead magnetic separator. An overhead magnetic separator has to pull ferrous material out of a burden through the air up to the suspended magnet. The suspension height puts a greater distance between the magnet’s face and the material to be separated necessitating the use of a larger magnet. A magnetic head pulley however, has the mechanical advantage of pulling ferrous material down to the belt at the magnet’s surface where its field strength is greatest. This may allow for higher belt speeds, resulting in increased production and productivity.
Magnetic head pulleys are best used in applications where the burden depth is shallow or in deeper depths when used in conjunction with an upstream crossbelt overhead magnet. This arrangement ensures that if a heavy burden depth causes tramp metal to be missed by one magnet, it will be caught by the other. One magnetic separator working on the bottom of the load and the other at the top. Dings manufactures three different strength series to accommodate varying burden depths and throughput volumes, Dings standard, heavy-duty and DFC Ultra.
Magnetic Deep Draw Drum Separators
Magnetic drum separators, such as Dings Deep Draw Drums, are another option for the remove of ferrous contaminants from wood and biomass product streams. Their operation is similar to magnetic head pulleys although they are not part of the conveyor belt directly. Instead material is discharged from the conveyor onto a rotating stainless-steel drum with a fixed permanent magnet inside of it. While the non-magnetic organic material follows a normal trajectory, the internal magnet holds any ferrous material to the shell of the drum until it rotates past the magnetic area discharging it underneath the drum. Due to their larger size, Deep Draw Drums allow for a heavier throughput than smaller magnetic head pulleys but cannot be used with a portable plants like head pulleys can be.
The Dings deep draw drum’s permanent magnet design outperforms electric-powered models in a number of important ways, it always operates at top efficiency and maintains a constant magnetic strength throughout the day. Deep draw drums employ Dings’ unique DFC (Dings Flux Control) magnetic circuit design that eliminates internal leakage between magnetic poles and improves separating performance. Other ‘conventional’ magnetic circuits contain air or filler material between the magnetic poles; this allows flux (magnetism) to escape (leak out) and be wasted. In Dings DFC design – blocking magnets are strategically positioned in the spaces between the magnetic poles. These redirect the flux outward, into the product, converting the wasted flux into working force -making the magnet more efficient.
SurroundScan Protector Series Metal Detection for Wood and Biomass Processing
Dings Co. Magnetic Group’s sister company, Advanced Detection Systems, engineers and manufactures metal detection systems. The Protector Series detects any ferrous, non-ferrous or stainless steel that made it past your magnetic separators. Metal detectors, when used with proper magnetic separation, complete the ferrous metal contaminant protection process. Or if metal is very rare in your process, a metal detector can be an economical and easy to install alternative to an overhead magnet or deep draw drum.
The Protector series metal detector will detect metal, alert workers and even shut down equipment before it can be damaged. The Protector’s steel construction and NEMA 4 electronics enclosure is designed for outdoor use and the removable end plate facilitates easy installation into existing processing lines. Protector series metal detectors are available as complete systems with splice sensors and metal markers
Which Magnet Separator is Best for Your Wood and Biomass Process? Dings Can Help
Dings Company Magnetic Group engineering and sales staff work together from our Milwaukee, WI factory to provide outstanding customer service from experts in magnetic separation. We listen to our customers to gain an understanding of their needs and apply our experience in their trade to provide magnetic separation equipment that is sized and positioned for the best possible performance in their specific application. Contact Us at magsales@dingsco.com or call us at (414)672-7830.