In aggregate and mining applications the need to remove ferrous often comes down to protecting processing equipment like conveyors, screens and crushers. Tramp metal, like bucket teeth, that get through can cause catastrophic damage and costly downtime while you’re forced to make repairs. The other benefit that magnetic separation provides is enhanced product purity.
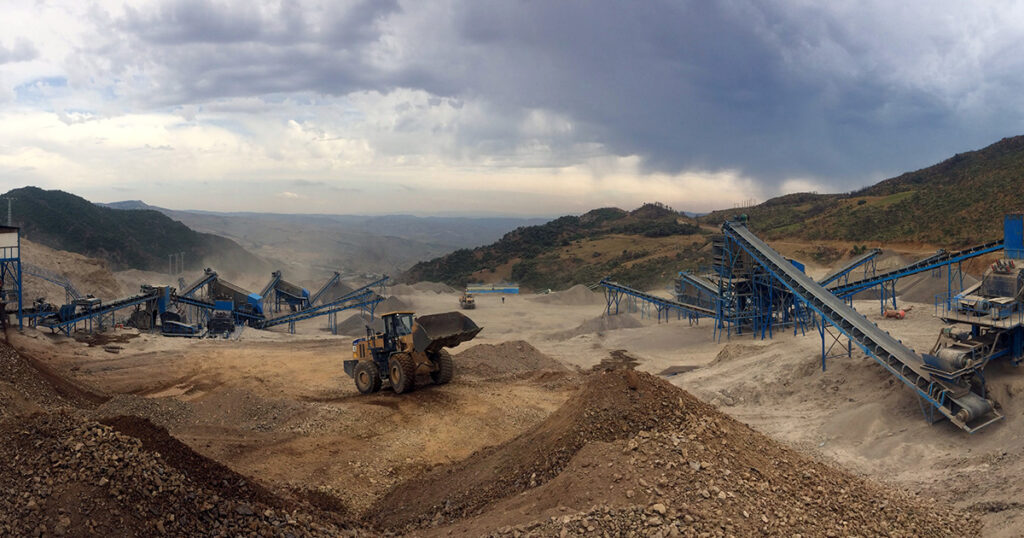
Overhead Magnetic Separators
Overhead Magnetic separators are often the best solution for removing damaging tramp metal in mining and aggregate production. However, when it comes to which type of magnet, that depends on the specifics of your application. How prevalent is tramp iron in your product? What type of product are you running? What is your burden depth? Is a lack of space above the conveyor an issue? These questions and more can be decisive in what magnetic separator solution is best for your mining application.
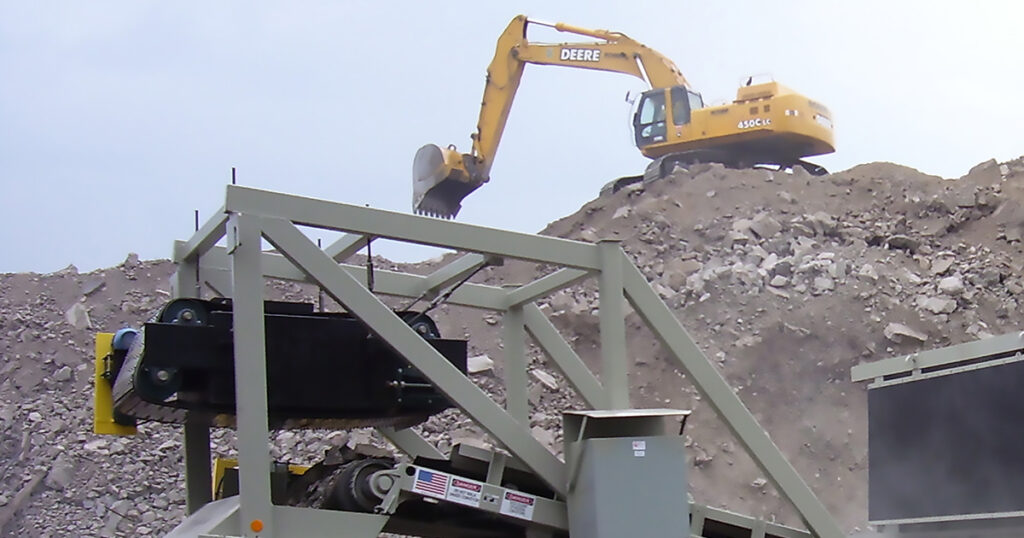
Self-Cleaning versus Stationary Magnets
Self-Cleaning Magnetic Separators
If tramp metal is prevalent in the mining or aggregate process a self-cleaning model might be best. A self-cleaning magnet uses a multi-ply rubber belt with 1-inch vulcanized cleats that travels across the magnet’s face automatically discharging the ferrous contaminants saving time and labor costs.
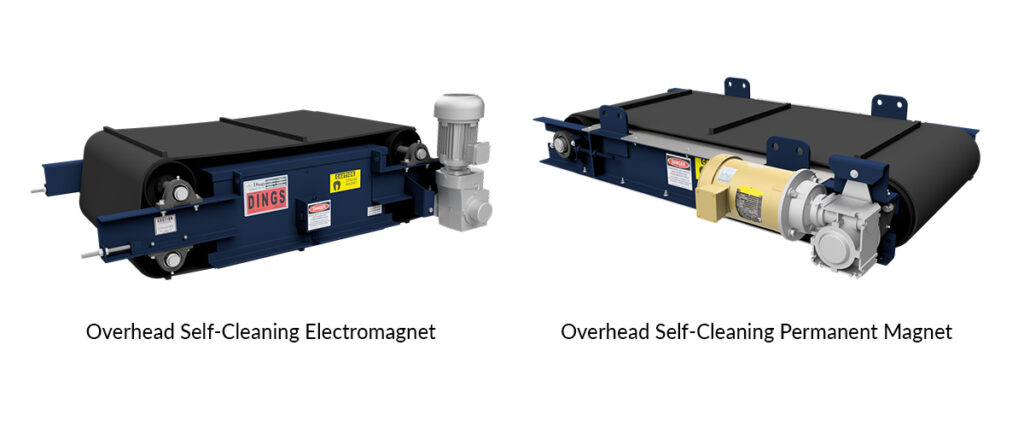
Stationary Magnetic Separators
If tramp metal is rare in the mining or aggregate process but intolerable, an overhead stationary magnet can be an optimal choice. Without having to accommodate for the sag of a self-cleaning belt in the suspension height, a smaller more economical magnetic separator may be possible. Stationary magnetic separators also don’t have moving parts or drive motors that can break down. This saves labor and repair costs while minimizing down time.
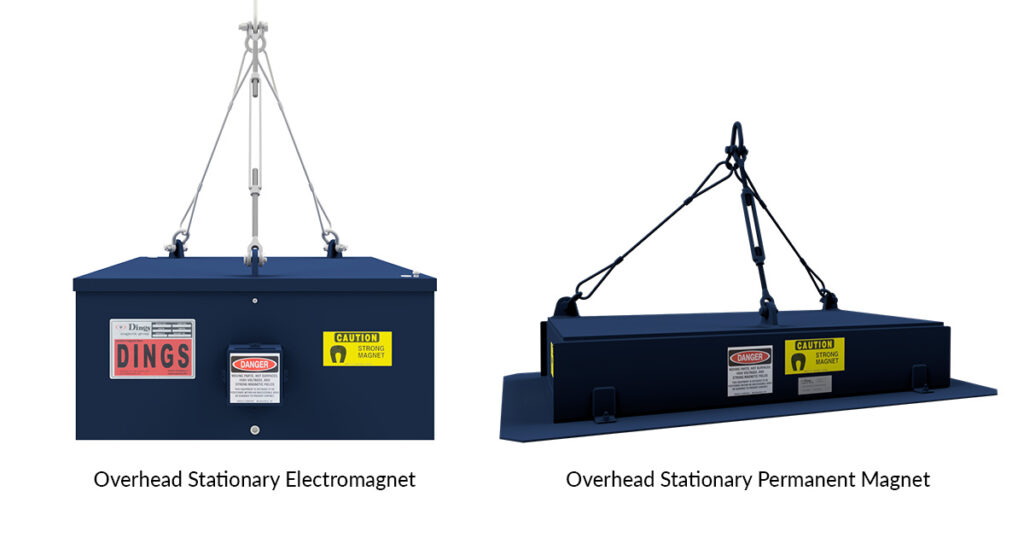
Permanent Magnets versus Electromagnets
Electromagnetic Separators
Electromagnets use electricity flowing through a coil structure around an iron core to create their magnetic field. Because of this, overhead electromagnetic separators allow greater control over the presence of its magnetic field. By simply cutting the power ferrous material will be released giving an electromagnet an advantage over the use of a permanent magnet in some mining and quarry applications. The deep toroidal shape of the magnetic field produced by an electromagnet can make it the magnet of choice for troughed belt conveyors.
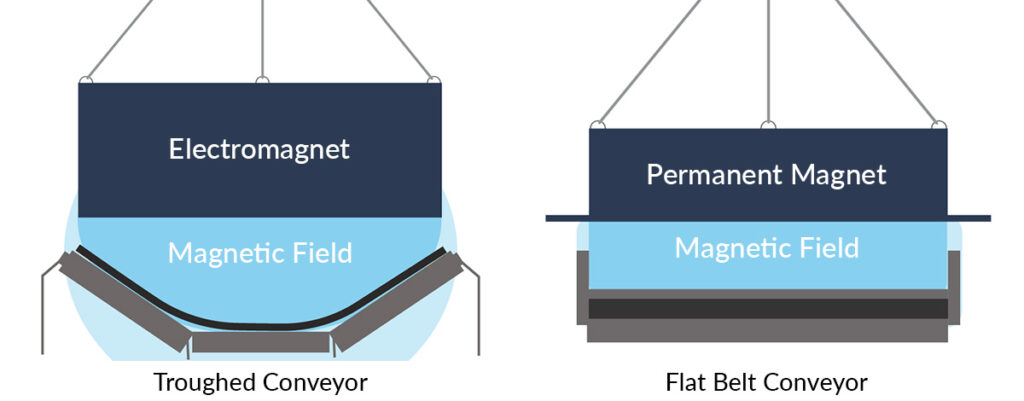
Permanent Magnetic Separators
Overhead permanent magnetic separators always have a magnetic field and don’t require any outside energy to produce it. Permanent magnets are more space efficient than electromagnets. This smaller size makes them ideal for use in tight spaces. However, because the magnetic field is always active, ferrous materials must be removed either manually or by use of a self-cleaning belt or other removal mechanism.
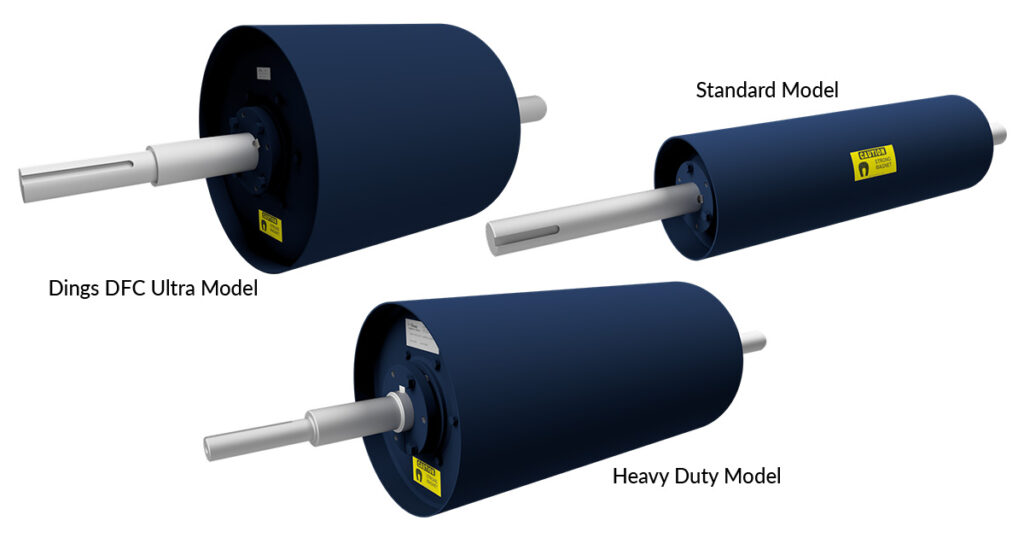
Magnetic Head Pulley Separators
Magnetic head pulleys are non-electric, self-cleaning magnetic separators. They operate as head pulleys on conveyors to separate tramp iron and iron impurities from conveyed product. They are designed for machinery protection and product purification. As the product is discharged from the conveyor, non-magnetic material follows its normal trajectory off the belt while ferrous clings to the magnetic pulley until it is released under the conveyor as the tramp iron leaves the pulley’s magnetic field. Dings manufactures three different strength series to accommodate varying burden depths and throughput volumes, Dings standard, heavy-duty and DFC Ultra.
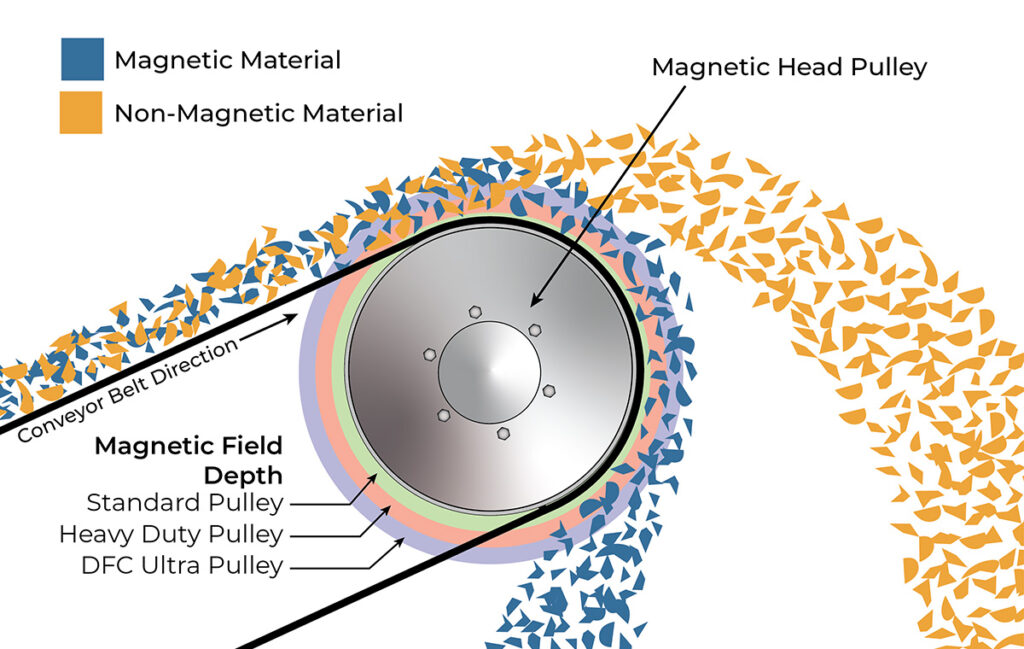
Which Magnet Separator is Best for Your Aggregate or Mining Process? Dings Can Help.
Dings Company Magnetic Group engineering and sales staff work together from our Milwaukee, WI factory to provide outstanding customer service from experts in magnetic separation. We listen to our customers to gain an understanding of their needs and apply our experience in their trade to provide magnetic separation equipment that is sized and positioned for the best possible performance in their specific application. Contact Us at magsales@dingsco.com or call us at (414)672-7830.