In recycling applications, there are many different types of material that need to be recovered. Magnetic separation equipment is ideal for pulling metals like iron and steel out of mixed material streams. However, non-ferrous metals like copper, aluminum, tin, and brass aren’t inherently magnetic, so normal magnetic separators won’t work. Therefore, an eddy current separator is often the best option to remove and recover these valuable non-ferrous metals. What makes an eddy current separator different from a normal magnet? How do they work? Let’s look into what an eddy current is, how they’re formed and how they’re used for separation.
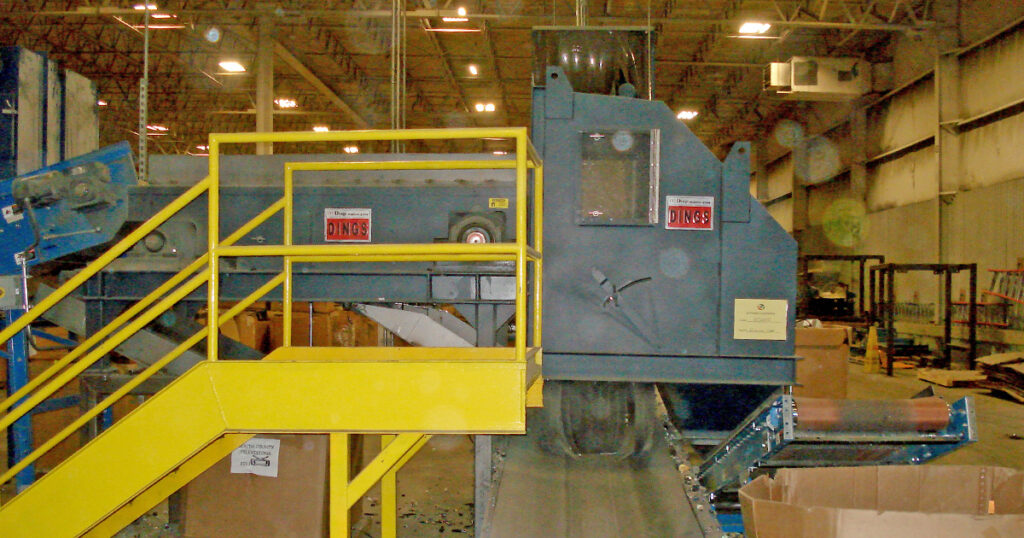
What are Eddy Currents?
When a changing or moving magnetic field is exposed to a conductive material, the change in magnetic flux creates an electrical current in the conductive material. This is in accordance to Faraday’s law of induction. The current flows in a circular motion around the magnetic field lines. This circular motion is what gives “eddy” currents their name, as they are reminiscent of whirlpools or eddies in water.
These electrical currents, as all electric currents do, create magnetic fields of their own that loop around the flow of electrical current. The magnetic field that is created is in opposition to the change in the magnetic field that created it as it tries to remain in balance as explained by Lenz’s Law. This means that the eddy current creates a magnetic field in the conductive material that has the same pole as the magnet that created it. As we know, two magnetic poles that are the same will repel each other. This property is how non-magnetic, electrically conductive metals can be easily separated from non-conductive materials.
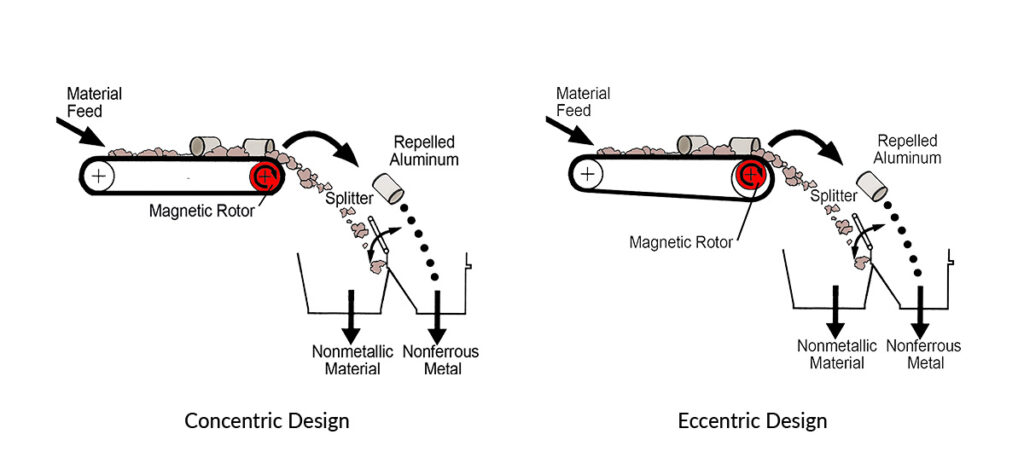
How an Eddy Current Separator Works
The key component of the eddy current separator is the magnetic rotor, which has a series of permanent rare earth magnets mounted on a support plate attached to a shaft. The magnetic rotor is surrounded by a wear shell that supports the conveyor belt. This allows the rotor to spin independently and at a much higher speed than the wear shell and belt around it.
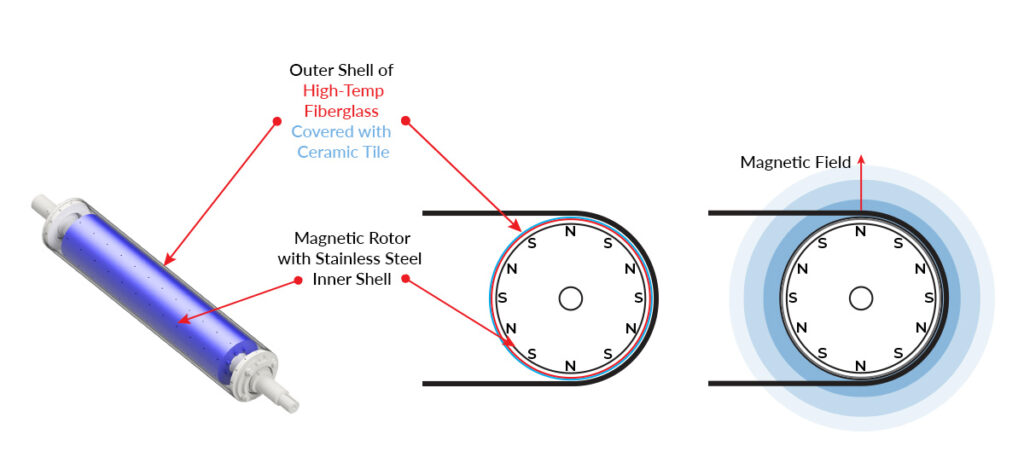
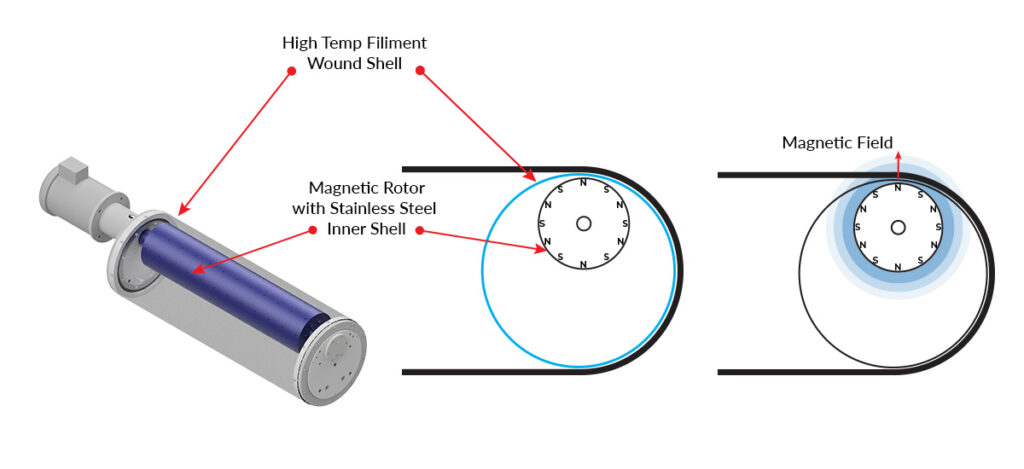
When a piece of non-ferrous metal (such as aluminum) travels along the belt and crosses over the separator’s rotor assembly, the magnets inside the rotor rotate past the aluminum at speeds up to 3000 rpm. Since the rotor is designed with multiple magnets in alternating poles the magnetic field can shift thousands of times per minute. As we discussed earlier, this creates eddy currents in the aluminum which, in turn, creates a magnetic field around the piece of aluminum. The polarity of that magnetic field is the same as the rotating magnet, causing the aluminum to be repelled away from the magnet. This repulsion makes the trajectory of the aluminum greater than that of the nonmetallic material, allowing the two material streams to be separated. An optional splitter is often used at this point to ensure that the that the two material streams are properly separated.
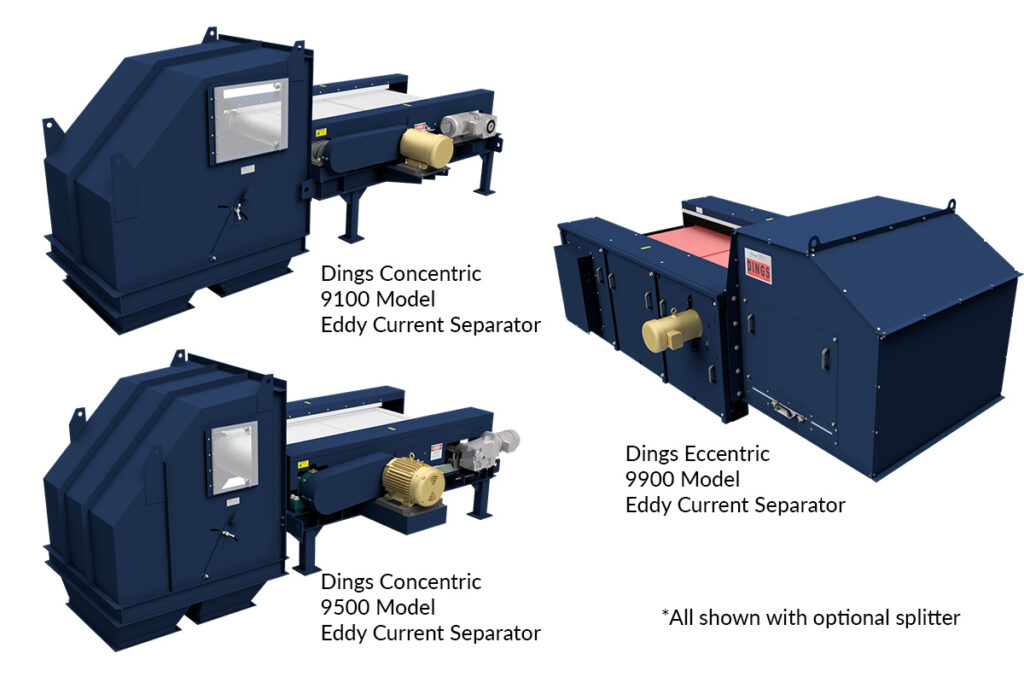
Dings Company Magnetic Group Helps You Find The Right Magnetic Separation Solutions.
Dings Company Magnetic Group engineering and sales staff work together from our Milwaukee, WI factory to provide outstanding customer service from experts in magnetic separation. We listen to our customers to gain an understanding of their needs and apply our experience in their trade to provide magnetic separation equipment that is sized and positioned for the best possible performance in their specific application. Contact Us at mailto:magsales@dingscoor call us at (414)672-7830.